Plastic Pelletizing Recycling Machine
InquireAbout Us
Polytime Machinery Co., Ltd. is a resource recycling and environmental protection enterprise integrating production and R&D, focusing on the manufacture of plastic product washing and pelletizing line equipment. Since its establishment in 18 years, the company has successfully implemented more than 50 plastic recycling projects in more than 30 countries around the world. Our company has IS09001, ISO14000, CE and UL certifications,we aim at high-end product positioning,and strive to develop together with customers. The purpose of the company is to save energy and reduce emissions and protect our common home earth.
OFFERS
Pelletizing line design for soft raw material is different from the design for rigid raw material
SOLUTIONS FOR SOFT RAW MATERIAL AS BELOW
LDPE /LLDPE /HDPE FILM/PP FILM/PP WOVEN BAG
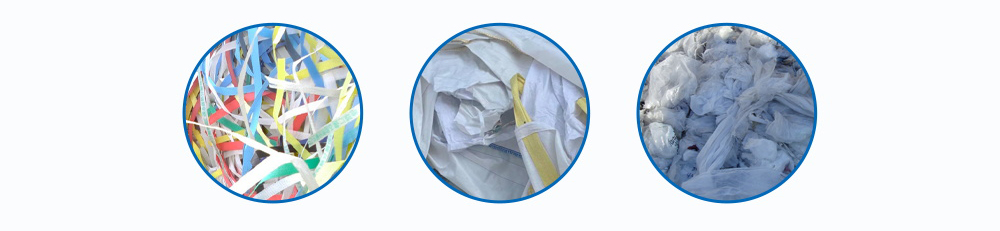
RIGID RAW MATERIAL AS BELOW
HDPE/ LDPE/ PP/ ABS/ PC/ PS/ PA/ PA66

The pelletizing line for soft raw material will be equipped with agglomerator normally, which is used for tear film into small pieces and then pinch it into a ball to rise efficiency of raw material feeding to barrel.
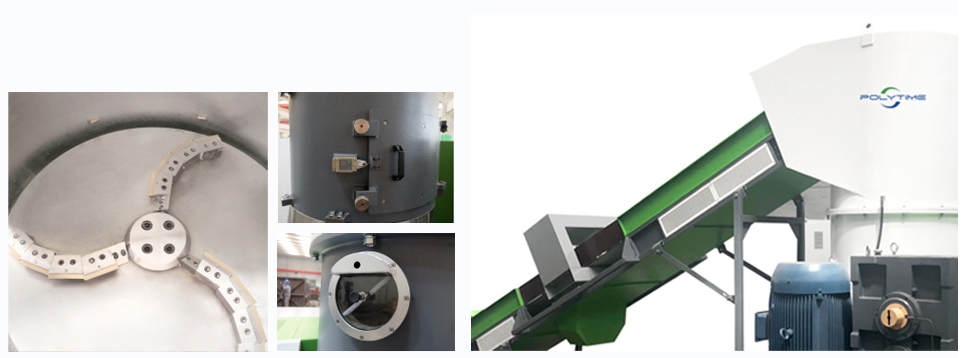
Bright spot(one line for 2 different kinds of raw material)
POLYTIME-M could provide the design for both soft and rigid raw material by one production line(Under certain conditions,for example customer could accept output capacity difference) 76%
- Technical Parameter -
Rigid Plastic Granulation Line
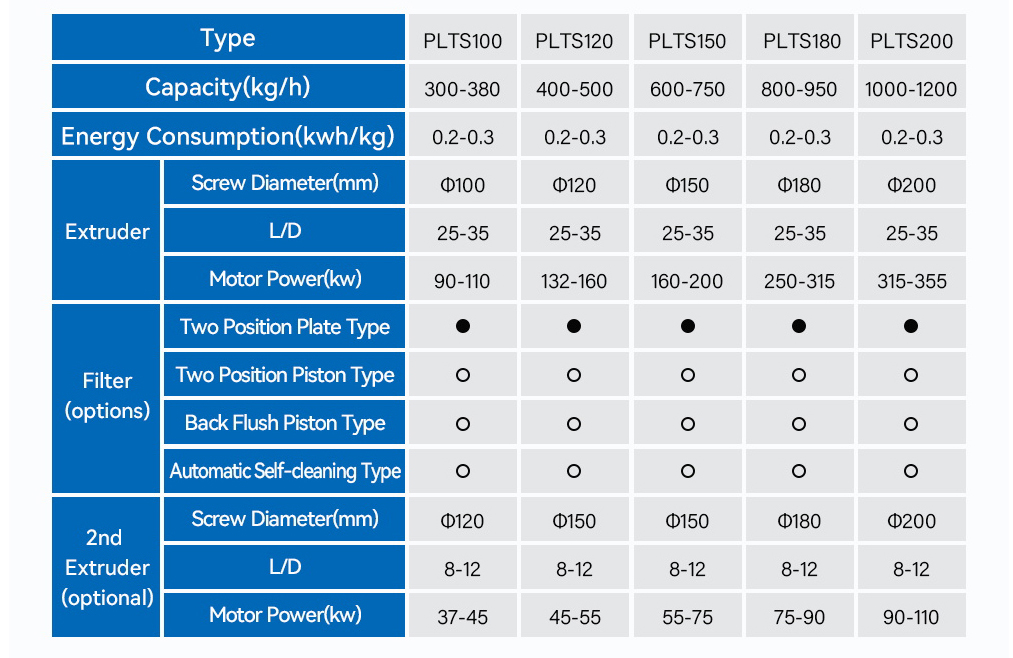
Soft Plastic Granulation Line
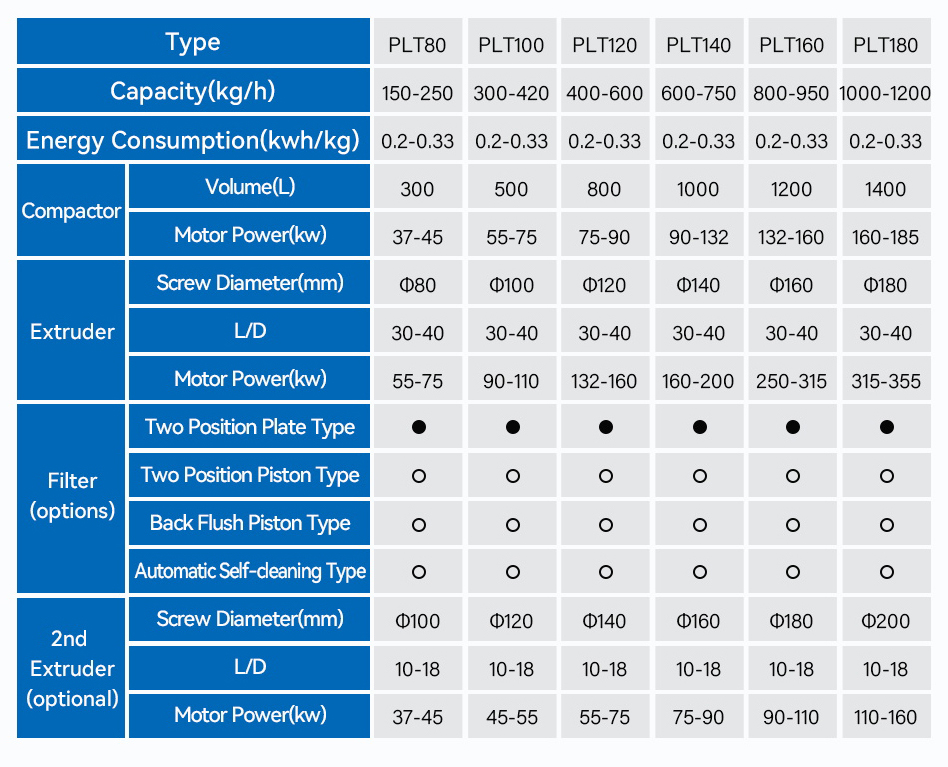
Single stage or Double stage?
Double stage granulation line is generally used for the raw material which after washing,it could bring 2 times degassing to get rid of moisture,also 2 times filtering to make pelletizing be more clean.
Single stage pelletizing line is used for clean raw material such as industry waste,including cutting edge of plastic package manufacturing.
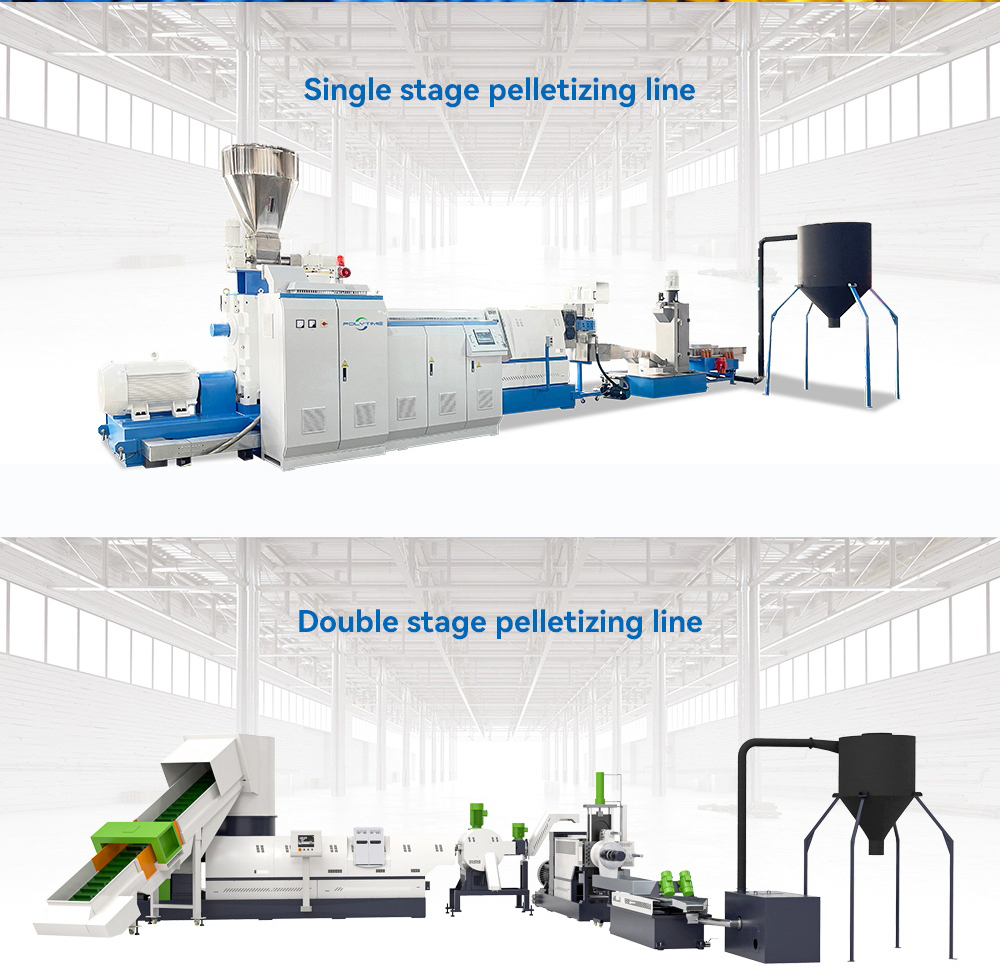
- Features -
CONICAL TWIN-SCREW EXTRUDER
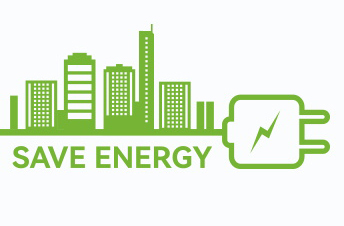
■ Servo motor, 15% reduction in energy consumption
■ PLC intelligent operating system, remote control
■ One-key start function, low learning cost
■ Pre-heating function to improve production efficiency
■ Feeding volume control system, matching various MFI raw materials
■1500kg/h MAX output capacity
■ Low vibration and low noise
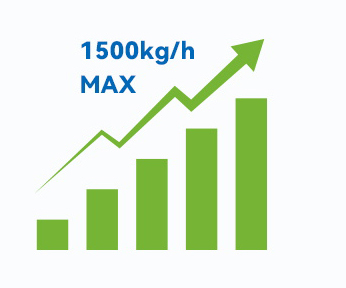
Production Line Structure Type
Single stage- Suitable
for Lightly dirty raw materials
Double stage-Suitable
for severely dirty raw materials
Cutting Type
●Water-ring cutting (Suitable for HDPE, LDPE, PP)
Polytime-M hot die face pelletising systems have undergone another stage of development. The focus has always been on straightforward handling and easy maintenance.
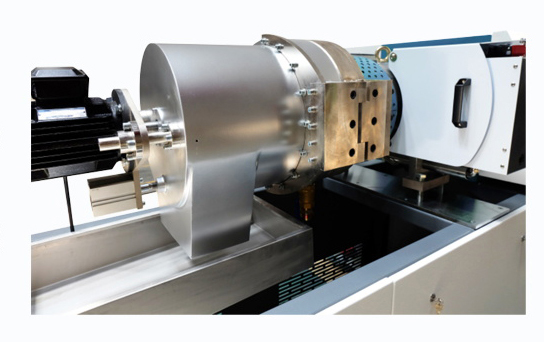
■Maintenance-free and smooth mechanical action of knife head pressure
■Knife head driveshaft with direct drive
■Outstanding cutting precision in combination with fully automatic pneumatic cutting pressure setting
■Pelletiser knives and die face have a long service life
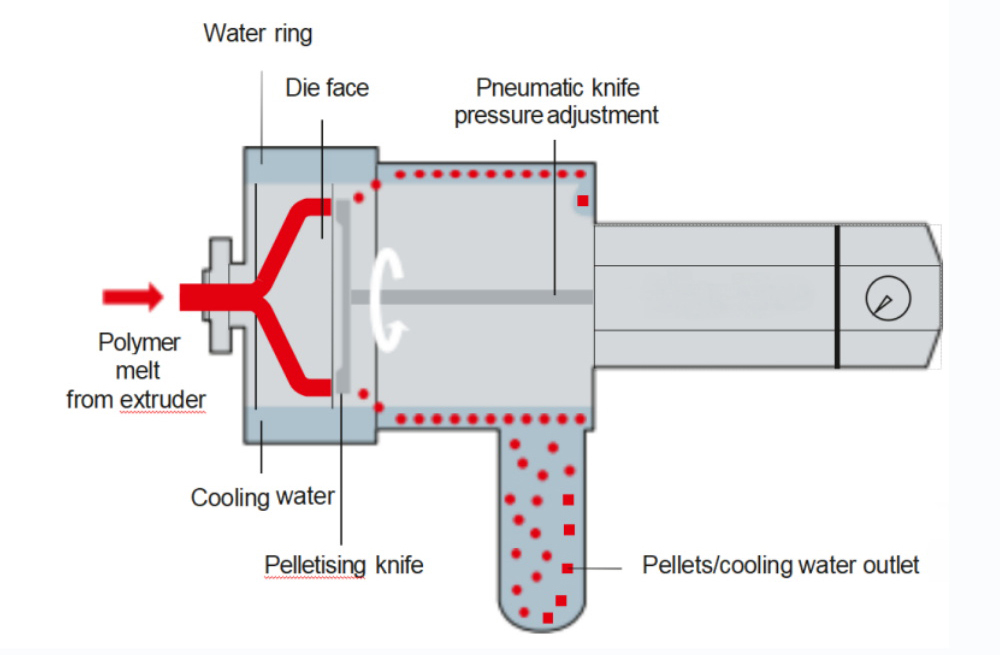
■Under-water cutting (PET recommended)
■Strips cutting (Suitable for various materials)
Screen exchanger
●Board double position hydraulic
Cheap cost, simple operation, but filtering area is not big
●Double column hydraulic screen changer
Cost is higher than board double screen exchanger, a lttle bit complicated operation,but much bigger filter area, it helps to decrease the frequency of replace filtering net.
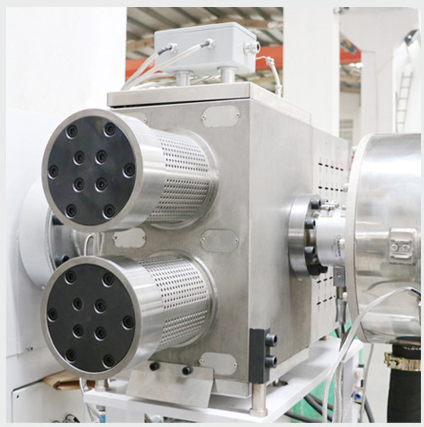
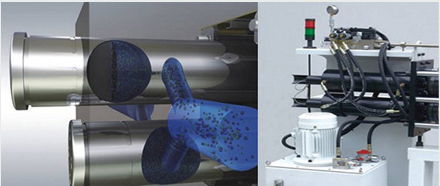
● Automatic laser filter
For primary filtering, it is generally installed on the first stage of pelleitizng line to remove big contamination, but investment is high.
Optimised pellet water removal screen with self-cleaning effect and easy-change filter cartridge.
Pellet centrifuge for enhanced drying performance featuring Direct Drive technology
Plower and noise protection integrated in pellet Centrifuge housing - compact downstream components
Folding housing cover on pellet centrifuge for simple cleaning when changing colours and straight forward maintenance
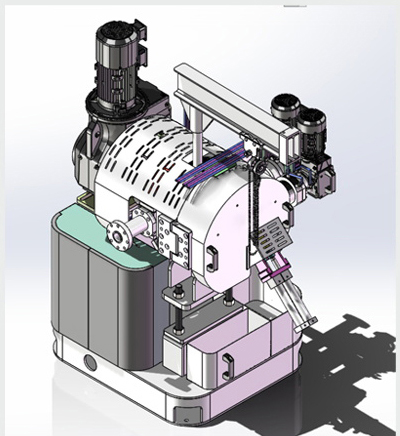
New pellet water separation screen
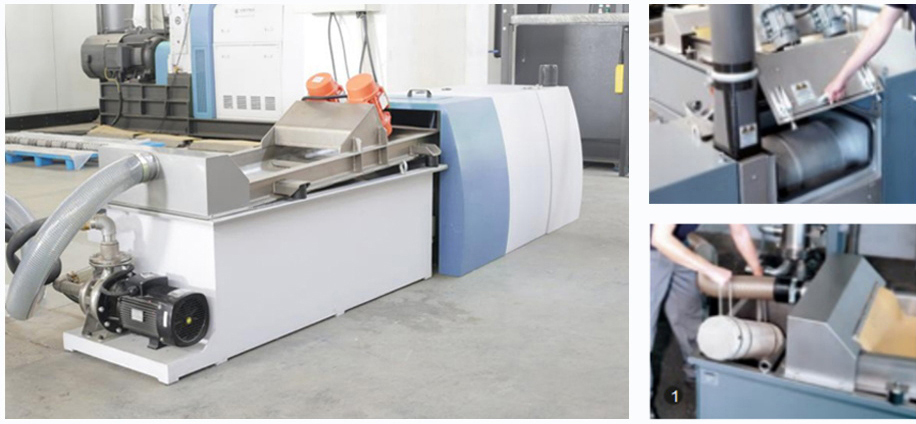
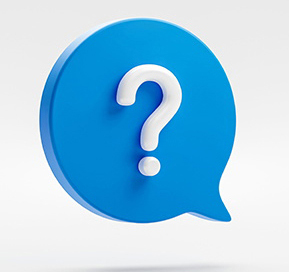
The questions to you before we offer
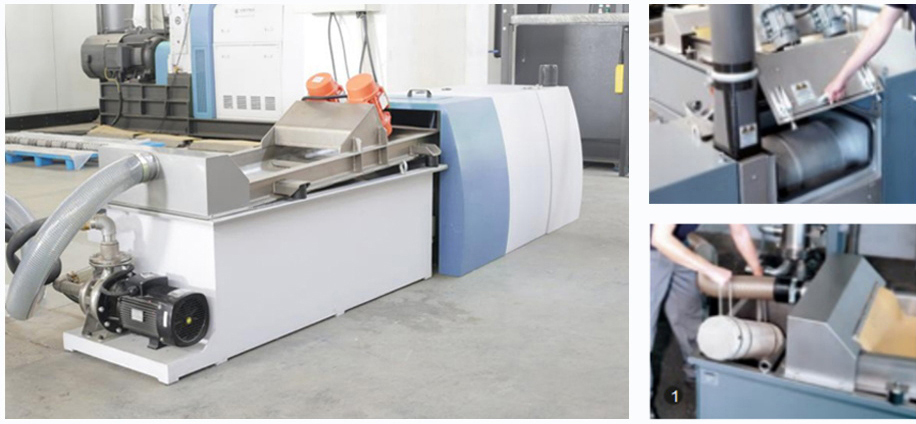
■What's the materia!?PP or PE,soft or rigid?
■Is the raw material clean or dirty?
■Is the raw material after washing?
■What is the MFI of raw material?
■Does the raw material contain with any oil and paint?
■Does raw material contain with any metal?
■What's the humidity of final pellets do you need?
■What's the application of final product?
■Do you also need a pelletizing line?
■Could you please share with us some pictures of raw material for better understanding.
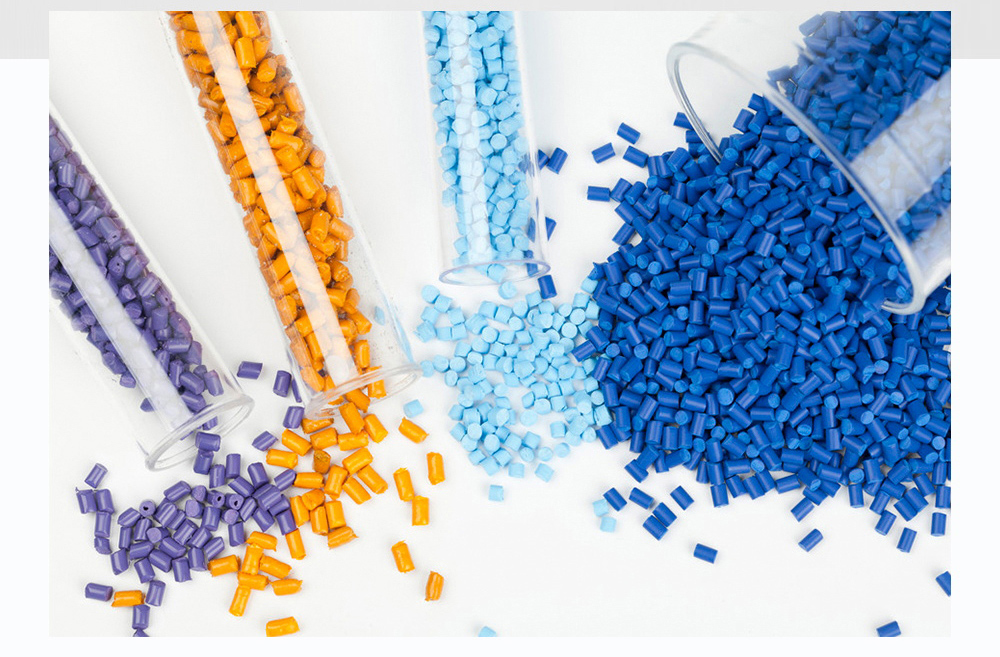
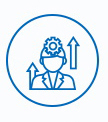
Technical Benfit
■Direct Drive technology with vibration-free design
■Lifetime lubrication of the drive shaft
■Very long pelletiser knife service life thanks to special cutting geometry and automatic pneumatic knife pressure
■Automatic pelletiser function supervision with alarm signal and automatic shutdown in the event of a malfunction
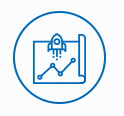
Economic benefits
■Suitable for use with virtually all standard extruders
●High degree of operational reliability and considerable reduction in maintenance costs
●Simple and rapid pelletiser knife changeover without adjustment work saves time
■Flexible arrangement of equipment downstream of pelletiser
■Reduced cooling water costs thanks to efficient pellet cooling system